The Role of Coating Weight in Electrolytic Tinplate: How It Impacts Your Manufacturing Needs
- szjqpack
- Oct 24, 2024
- 4 min read
Choosing the right materials for manufacturing is crucial, and when it comes to electrolytic tinplate, one of the most important factors to consider is coating weight. The coating weight plays a vital role in determining the tinplate’s durability, resistance to corrosion, and its suitability for various applications, particularly in packaging. Understanding the role of coating weight in electrolytic tinplate can help you make the best decisions for your manufacturing needs.
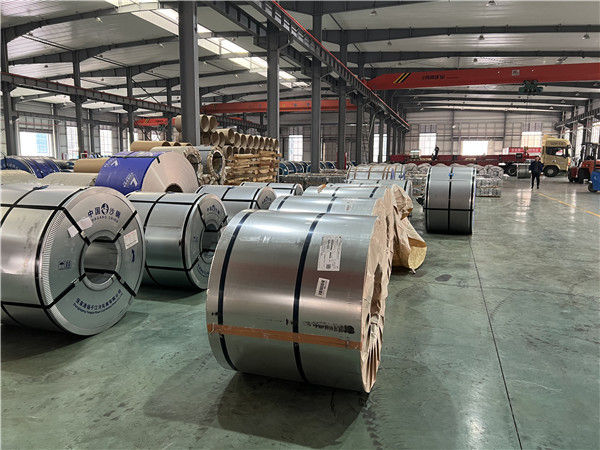
What is Coating Weight in Electrolytic Tinplate?
Coating weight refers to the amount of tin applied to the surface of the tinplate during the manufacturing process. This tin coating is what gives the electrolytic tinplate its corrosion-resistant properties and helps preserve the integrity of products, especially in tinplate for packaging applications like food, beverages, and chemicals. The coating weight is measured in grams per square meter (g/m²), and typically, the higher the coating weight, the more protection the tinplate offers. However, this protection depends on the specific needs of your manufacturing process, which is why choosing the right tinplate coating is essential.
Why Coating Weight Matters for Your Manufacturing Process
The coating weight in electrolytic tinplate is significant, as it directly impacts several aspects of your manufacturing process, such as durability, corrosion resistance, and product appearance. Whether you’re producing food cans, chemical containers, or automotive parts, the coating weight can affect the lifespan and reliability of the end product. For instance, heavier coatings provide greater corrosion resistance, making them ideal for products that require long-term storage or exposure to harsh environments. On the other hand, lighter coatings might be more appropriate for products that don’t face the same environmental stresses, allowing for cost savings without sacrificing performance.
Understanding the Role of Coating Weight in Electrolytic Tinplate
The role of coating weight in electrolytic tinplate is a critical factor in determining how well your products are protected during manufacturing and throughout their lifecycle. The tin coating applied to the steel substrate is what gives electrolytic tinplate its corrosion-resistant properties, which are essential in various industries, particularly packaging and food preservation. In essence, coating weight refers to the amount of tin deposited on the surface of the tinplate, typically measured in grams per square meter (g/m²). The thicker the tin coating, the more protection it provides against rust, oxidation, and environmental wear and tear. This becomes especially important in applications such as tinplate for packaging, where exposure to moisture, acids, and other elements can compromise the quality of the contents. For example, canned goods and beverages benefit from higher coating weights to ensure long-term freshness and protection.
The coating weight in electrolytic tinplate also extends beyond just corrosion resistance. It impacts factors such as weldability, formability, and aesthetic appeal. Products with a higher coating weight generally exhibit better resistance to mechanical stress, making them ideal for high-demand applications in industrial settings. Conversely, a lighter coating weight might be preferred in applications where cost efficiency and lightweight properties are prioritized, such as in certain consumer goods or short-term storage solutions.
Coating Weight Selection Guide: How to Choose the Right Tinplate Coating
When choosing the right tinplate coating, it’s important to understand the specific requirements of your industry and application. Here's a quick coating weight selection guide to help you make the best choice:
• Heavy Coatings (e.g., 5.6 g/m² or higher): Ideal for corrosive environments or products that need to withstand long-term exposure, such as food cans or chemical packaging. These provide maximum protection and durability.
• Medium Coatings (e.g., 2.8 g/m² to 5.6 g/m²): Suitable for packaging that requires a balance between protection and cost-effectiveness, such as beverages or canned goods.
• Light Coatings (e.g., below 2.8 g/m²): Best for products that don’t require extensive protection, such as certain automotive parts or short-term storage containers. These coatings are more economical while still offering adequate performance.
This coating weight selection guide ensures that you get the most value and performance from your tinplate, tailored to your specific manufacturing needs.
See the full story: Ultimate Choice for Tinplate Coil Packaging
Industrial Tinplate Coatings: How They Vary by Application
In industrial manufacturing, industrial tinplate coatings are not one-size-fits-all. Different industries have varying requirements when it comes to coating weight. For example, the tinplate for packaging in the food industry must adhere to stringent regulations to ensure product safety and longevity. Meanwhile, industrial tinplate used in automotive parts must provide robustness and resistance to wear and tear. The thickness and type of coating required for your product will depend on factors such as exposure to moisture, chemicals, and environmental conditions. Heavier coatings are typically used for packaging that will come into contact with corrosive substances, while lighter coatings are ideal for applications where cost-efficiency and minimal exposure are priorities.
How to Optimize the Coating Weight for Different Manufacturing Needs
To fully optimize the coating weight in electrolytic tinplate, it’s important to align the coating with your specific manufacturing requirements. Consider the following steps to optimize your process:
• Assess the environment your product will face: If your product will be exposed to moisture or corrosive substances, opt for a higher coating weight.
• Understand your product's lifecycle: Products with a longer shelf life or that require long-term durability, such as food containers or automotive components, benefit from heavier coatings.
• Balance cost and performance: While heavier coatings offer more protection, they come with a higher price tag. Determine the minimum coating weight that meets your durability needs without overspending.
By following these guidelines, you can ensure that your tinplate selection is optimized for both performance and cost-efficiency.
Conclusion
The coating weight in electrolytic tinplate cannot be understated. It affects everything from product durability to the ability to resist corrosion in various industrial applications. By understanding how coating weight impacts your manufacturing process and choosing the right tinplate coating for your needs, you can ensure optimal performance, cost-effectiveness, and product safety. Whether you’re manufacturing food cans, automotive parts, or packaging materials, the right tinplate coating can make all the difference in the success of your products. Use this coating weight selection guide as a reference to make informed decisions that meet your specific manufacturing requirements.
Comments